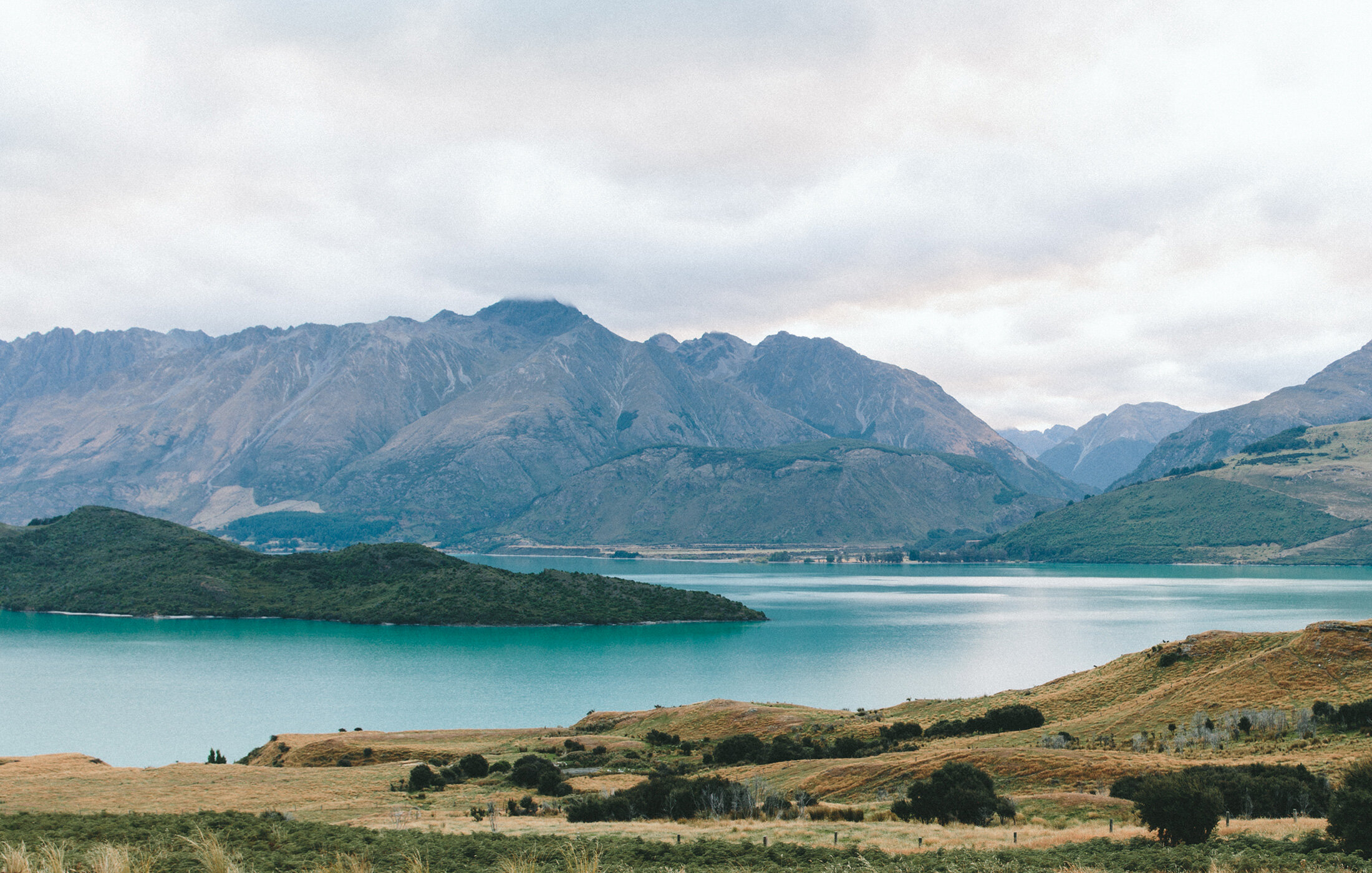
Declan
Posters for Fall 22 and Spring 23
Despite the website being down for half of this academic year, much progress was made on my project this year. Click the icon to read the posters for the WISRD Physiology Group this year, as well as posters from past years.
Journal entries imported from the previous iteration of wisrd.org
DECLAN
Week of April 11th:
This past week I have been synthesizing the theoretical aspect of our rocket. I have been able to complete some of the math, but not all of it. We are sending what math we have to Daniel Krashen, a professor at the University of Georgia.
Our ultimate goal is to maximize impulse. We want to be able to graph the relationship between water and air in the rocket and impulse. We show what this graph should look like in the attached graph.
We began using Bernoulli’s principle to find a relationship between the exit velocity and pressure.
We solved for exit velocity.
We then used the ideal gas law to solve for volume.
We then substituted the the derivative of volume to find the change in mass over time.
(Above is the expected relationship between impulse and ratio of water/air)
Week of March 14th:
This past work I’ve been working mainly on the theoretical aspect of our rocket. I am working to determine the optimum amount of water and pressure inside the bottle rocket. I am comparing these values against the theoretical impulse of the rocket. This is a very difficult project to undertake, but I believe that with some help I will be able to come up with, at least, one theoretical value. I have spoken with Scott about this problem and he has agreed to, as part of our physics class, show us a rocket problem in class.
After finding these theoretical values we are going to launch our rocket (provided that the launch mechanism is complete) with the PSI and amount of water that I have found. Hopefully, we are going to reproduce the launch multiple times with varying PSI’s and water levels to see if my theory holds true. I assume that there will be some error in my theory, as I will have to make some assumptions about the rocket and it’s properties to keep the math from going beyond singe variable calculus.
Week of March 7th:
This past week I was able to hear from the other members of the institute on the projects that they have been working on. I was also able to present on my project with Jacob and Nanak. I found it very interesting and informative to hear how the other members were doing and what they were working on. I especially enjoyed the ReefQuest presentation, and was impressed with Dylan’s ability to communicate ideas. I also thought that it was interesting how he is creating a system in which many people will be able to help analyze the wellbeing of reefs as opposed to a single individual.
I believe that my own presentation went rather well also. We talked about our ideas over the past work as well as those we have been doing over last semester, but focused mainly on our work this semester. I gave an overview of the bottle rocket that we are using and the method by which we are going to measure the velocity , acceleration, and height of the rocket. Jacob then talked about the design for our launch pad, as well as the problems that occurred with our previous launch method. Nanak then gave an overview of our wind tunnel design, and emphasized the importance of understanding how the rocket will perform as it travels through the air. Overall, it has been a great learning experience talking about my work and listening to others. I have learned how to better communicated my ideas to others through this experience.
Week of Feb 29th:
This past week we’ve been preparing for our presentation to the rest of the Institute, which will be early next week. We know that we will be talking about our learning objectives, background information, what we’ve been working on, specific details of what we’ve been working on, and what we plan to do in the future. Based on what we do in class, we have decided that I will talk about background information, learning objectives, and the design of the rocket. Jacob will take the lead on talking about our launchpad failures and our new launchpad design. Jacobs will also talk about the process of creating the design in SketchUp, which was a new learning objective for us. Nanak, who has been working relatively independently on creating our wind tunnel and wind tunnel accessories, will be talking to the institute about that.
Week of Feb 22nd:
This past week we’ve been able to CNC a large portion of the pieces necessary to build our launchpad design. Thus far, we have CNC’ed the bottom of the launchpad, which we are calling the baseboard, as well as the sides of the body. All we have left to CNC are the arms of the release mechanism. Moving forward we plan on printing this last and pivotal piece within the next week. We also feel as though we should, for sustainability purposes, CNC our next version of this launchpad in metal as opposed to wood, which is what we’ve been making it out of thus far. This has been a great learning experience for me because I have never had to work with such a device before. It also has given me the opportunity to learn about different materials and their strengths and weaknesses. For example, I had to see whether or not each material (we ended up deciding on aluminum) could withstand the force of our rocket launch.
Week of Feb 15th:
Last week we were able to convert our sketchup file to SVG, but one of the axis was misaligned. This week we focused on fixing this very problem. We went back into the original sketchup file and took new focused that were aligned correctly with the axis of direction. We made sure the the birds eye photo, which was the one that caused us problems previously, was exactly parallel to the x-axis. Once we accomplished this, we exported those photographs into another PDF file, which was then converted to an SVG file using the same website as last time (https://image.online-convert.com/convert-to-svg). We then uploaded this file (which represented our design accurately this time) to Easel and began the process to start CNCing the launchpad.
This past week I also focused on determining, based on the dimensions and water content of our bottle rocket, how much force the launch pad will have to withstand. For these calculations I assumed that the bottle will be filled with 700mL of water and be pressurized to 40 psi.
I determined that the mass of the rocket = 0.6986 kg.
The flow rate therefore is 7.2302 kg/s
The exit velocity is 20.927 m/s
The thrust is 151.3 N
So we now know that our launchpad needs to withstand more than 151.3 N of force.
Week of Feb 8th:
This week we (Jacob and myself) focused on converting our launchpad sketchup design to an SVG file so that we will be able to create the model through our CNC machine with the help of Harry. We tried multiple ways of doing this: we installed a plug in to sketchup and attempted to export the file as an SVG, we tried exporting the file as a .DWG and then converting that file to an SVG using an online conversion website, and, after repeated failure, we attempted exported the file as a PDF and attempted to convert the file using the following website (https://image.online-convert.com/convert-to-svg). We were successful in converting the file to an SVG, but the angle that we converted the file to from the PDF was off. When converting from a PDF we have multiple photographs from the different axis of direction. One of these photos was off, making the SVG file incorrect in its representation of our design. We will continue this work next week and update accordingly.
Week of Feb 1st:
This past week Jacob and I focused on creating the final design for our launchpad. Joe told us that another teacher already had a premade launchpad, but we have some reservations about how well it is going to work. It doesn’t seem like the design that was provided for us will be able to hold water, as the hole that creates the airflow into the bottle doesn’t seems able to hold water. Nonetheless we are interested in using it while we continue designing our own launchpad. This will allow us to gather some data on velocity, acceleration, drag, etc. while building our final design. I’ve learned to compromise on certain aspects of the project while still moving forward towards my final goal. In this way, I have found that, more important than moving forward as fast as I can, is my understanding of the concepts underlying the project as a whole.
In sketchup we are taking the design apart piece by piece so it will be easier to CNC. We moved one of the hooks that holds the rocket in place to the other side of the design. We can now CNC two identical pieces that, when placed together, create the full launchpad. Basically, we did everything we could to simplify our design while still maintaining its integrity. I had never simplified such a complex design before. This was a new learning for me.
We also worked on the mechanism that pumps and holds pressurized air in the bottle itself. We know that we need to create a hole of 5/8 inch diameter in the middle of the platform, but we have not finalized the design for the pump itself. The leading idea, which is also the most simple, is just to put the valve in the hole and hot glue it. This will both save money (we have all the pieces), time (it’s simple), and work (not a lot of physical work would need to be done).
Week of January 25th:
This week in Advanced Topics we focused on designing a better launching mechanism for our bottle rocket. We want this to be something that will create reproducible and constant results. This idea came about because our previous launch mechanism (waiting for the rocket to blow from the pressure) wasn’t reproducible. Our new mechanism will be able to release the rocket at any PSI we want consistently. The main research involved for this process concerned aluminum milling. I learned that I would need to set the drill to a lower RPM (which Jacob showed me how to do) and lubricate the drill piece. But, Jacob later told me that it could be easier just to CNC the pieces.
The design for this launch mechanism is built using 1/8′ this pieces of aluminum sheet. We first designed it on a whiteboard but decided that we better use something more seriou. Jacobs worked on a sketchup of what this would look like (you can see this on his reflection). The mechanism that we designed works as both a station to pressurize the rocket as well as release it. Four teeth hook on to the lip of the bottle a couple centimeters above the cap and release simultaneously, letting the rocket fly off. In this way we can release the rocket at any PSI we want, making our research more quantitative.
Week of January 18th:
This week our group tested differing nozzle designs and launch mechanism for our water rocket. The first design that we tried was an inner tube from a bicycle tire, which was wrapped around the valve (which connects to the air pump). We connected this valve to an electric air pump (which was provided by the PE department), and waited until the building pressure forced the rocket into the air.
We later decided that this was not the ideal form of launching the rocket, and instead drilled a 5/8 inch hole into the cap of the bottle (which is a naturally better fit). We stuck the valve from the bike tire about a half inch deep into this hole, filled it half full of water (750 mL), and waited for the pressure to force the rocket off again. In this instance a blast shield was used for protection because the pressures were much higher. After roughly 40-50 seconds we heard a loud noise, which was the top of the bottle exploding from the pressure. Our conclusion was that the valve was stuck into the cap too tight, causing the pressure to build too high before the rocket launches. Our next attempt is to push the valve in less (about 1/4 inch) or to create a mechanism that releases the rocket manually without having to wait for it to release itself. This is more ideal as it allows us to regulate pressure.
We are also hoping to record our flights with a string attached to the rocket. This will allows us to study the velocity, acceleration, change in mass, etc. of the rocket. This will give us the opportunity to mathematically predict the velocity, etc. of the rocket at any given point.