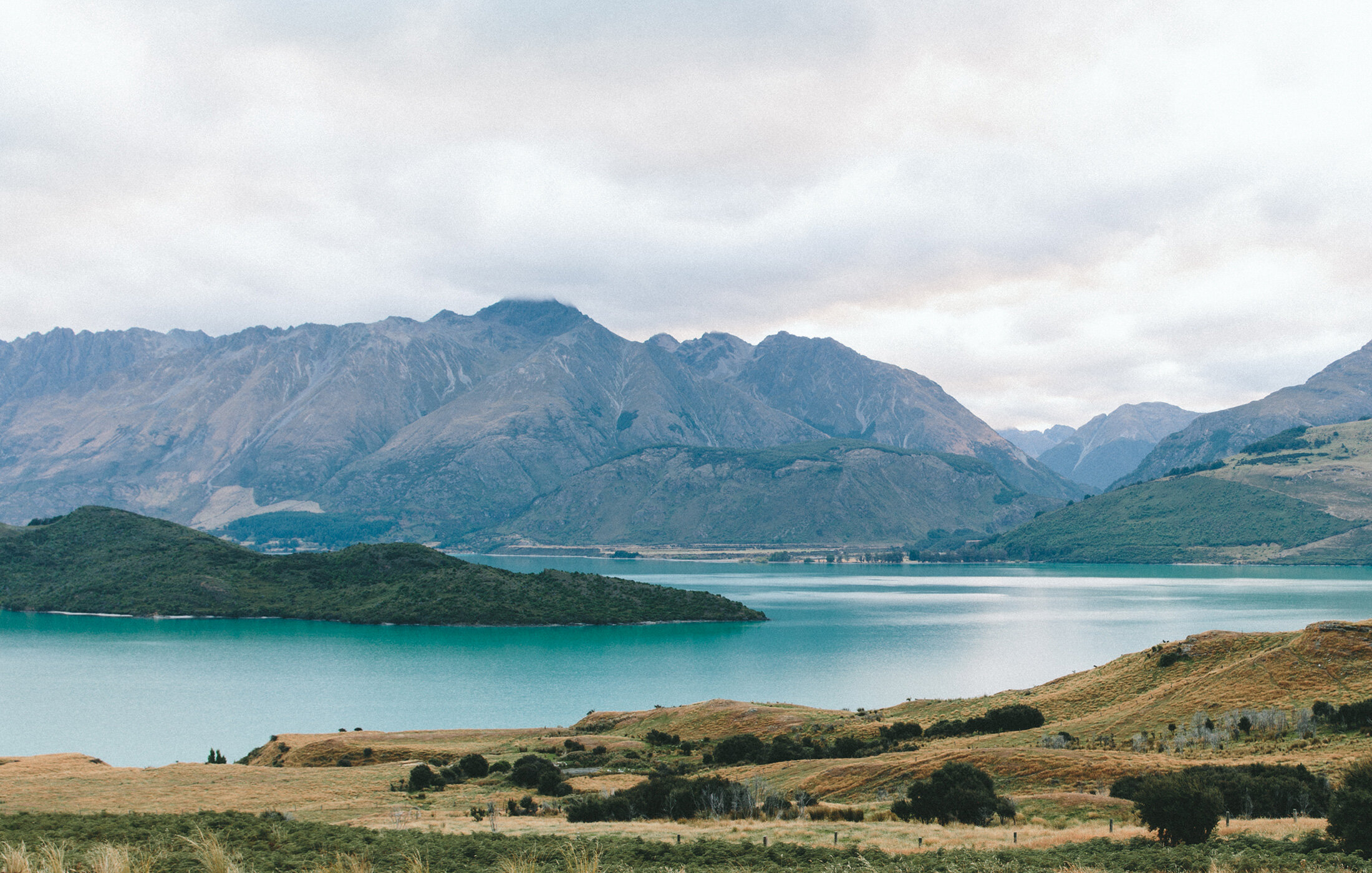
Emily R.
Posters for Fall 22 and Spring 23
Despite the website being down for half of this academic year, much progress was made on my project this year. Click the icon to read the posters for the WISRD Physiology Group this year, as well as posters from past years.
Journal entries imported from the previous iteration of wisrd.org
EMILY R.
Update – April 24th, 2019
My Emotiv Handbook is complete! As I will be going to college next year, I have compiled helpful data and information for those who will follow my work after I leave. It can be found here.
Update – February 29th, 2020
InnovatED.LA was a huge success! The turnout was incredible, and I’ve never seen kids as actively involved as they were this year. After presenting Emotiv to a rising freshman, she was so interested that she asked me to tour her through the WISRD lab and see the work we had done. Her and her mother were blown away by the work we were doing as high schoolers, in awe of WISRD, and hooked on joining next year. I was also in contact with the Wildwood admissions team, and reached out to incoming Wildwood students to speak about my WISRD experience. The response was also incredible, and gives me hope for the continuance of great WISRD leaders after the seniors leave.
Update – February 4th, 2020
Due to constant research with Emotiv, I haven’t been working with printers as often. However, the Makerbot stopped extruding from the right today, and I couldn’t wait to repair it! The filament was not stuck in the nozzle, but instead, between the middle heater. Someone must have begun a change in filament process, and stopped halfway, because the filament had been sucked up and then clogged. It was a simple fix, and the printer is back up and running.
Update – January 26th, 2020
We recently have been checking in on Zaniyah H., who has been working with e-NABLE. Our verification on the chapter map had disappeared, and we eventually contacted e-NABLE to re-demonstrate our credentials. We are now live on the map again, and taking new orders! Re-verification just must happen each year.
Update – January 15th, 2020
We have continued analyzing EEG data, and working to understand the individual EEG waves. When the waves are looked at in pairs, it is clear how much they interact. When stress rises, it creates shifts in the other waves as well, in a complement to one another. We are continuing to note more specific comparisons for our research!
Update – January 7th, 2020
For the past month, I have been working on my white paper, interspersed with minor tests to keep up the headset data. It is finally finished and will be published by WISRD! This paper focuses on the background and previous research done in stress studies. One major study on stress in high school students was performed in Mexico, but it was an observational study. Another Australian study surveyed thousands of students and analyzed their results. Interestingly, however, most stress studies are done through survey, because it is “more convenient” than reading brainwaves or doing a brain scan. It is not the most accurate, but there are some interesting results that have been gathered over the years. I’m excited to add my own research to the paper, once our study is complete!
Update – November 22nd, 2019
Today I had a successful test on Steveen G.! I recorded his brainwaves and took a video of the screen and him so peaks in stress could be directly correlated with his actions. After recording his baseline, Steveen G. was put through three tests. First, he recited the alphabet backwards. Stress wobbled up and down throughout, and as he took deep breaths, stress levels decreased. Then, he was asked to write a story in Spanish. His stress levels stayed low. Next, he had to solve statistics problems, and his stress fluctuated again, with deep breaths being successful regulators of this stress. Interestingly, however, whenever a certain teacher’s name was mentioned, his stress hit almost maximum peak. Deep breathing did not calm him down. For privacy purposes, the video will not be put up. However, it is important to note that this academic-environment-specific aspect increased stress so heavily.
Update – November 19th, 2019
Dark Matter Day was a success! There were fall themed activities, and younger students were very interested in 3D printing and VR. Seeing such young people so involved in the WISRD community was incredibly exciting and provides a lot of hope for the future!
Update – October 25th, 2019
We had our poster presentations last night! Grace K was our test subject during presenting. We were able to gather continuous data, and viewers were very impressed! They were astonished that they were able to see what was going on in Grace’s mind. However, we learned that connectivity decreases on smaller head sizes, and overall, females tend to have smaller heads than males. We need to figure out a way around this problem, to gather variable data.
Update October 14th, 2019
We’ve been continuously testing and working to analyze data we’ve already tested. High beta waves in the C3 section measure stress. Upon looking at data, there is clear growth and drop in the high beta. That’s amazing for analyzing our results, as differences are quite clear!
Update – October 10th, 2019
Our Inquirer(WISRD Journal Publications) entry is finally ready to be published! I’ve been working on writing, rewriting, and reconstructing this article for weeks, and it will reach the public soon! It focuses on the stress of high school students, between public and private schools. It also notes confounding variables that interfere with stress.
Update – October 6th, 2019
We have been able to record data, and we’re now interpreting it! We have figured out that F=frontal, Fp=frontopolar, T=temporal, C=central, P=parietal, O=occipital, and A=auricular (ear electrode). We’re currently attempting to analyze our data given this information.
Update – October 3rd, 2019
We’ve discovered that in order to ensure the best contact quality, we must dig a screwdriver into the holes holding the gel. We’re consistently reaching 60% on average, which is a great improvement.
Update – September 30th, 2019
Upon reading more articles about connection processes, some individuals using this headset say water will negatively impact connection. We tried to connect without a wet head, and gained less than 15% connection. We tried again with water, and reached 100% connection for the first time. There are a lot of conflicting and confusing ideas present, so we have to complete a different type of test before recording data.
Update – September 27th, 2019
We tried the same process using ethernet, and were hit with the same results. No stronger connection was present. There must be another connection issue, unrelated to internet.
Update – September 25th, 2019
After the first successful connection, we are struggling again. Every time the headset is set up, it doesn’t connect until 5-10 resets of system. A message appears either reading “connection lost”, “cannot connect”, or “lost API”. Upon connection, connection percentage bounces back and forth between 50 and 0. Sometimes, connection doesn’t even pass 25. The same procedure is followed the same every time, the test is done in the same spot, on the same person, yet the results are different. We’re going to try a test through ethernet as we think the wifi connection could be poor?
Update – September 23rd, 2019
Finally, we tested with gel! We followed the gel setup video from our Emotiv contact, seen as: https://www.youtube.com/watch?v=64qlwZwAIzw . However, we only began receiving 50-75% connection, and even then, connection bounced back and forth. It was continuously unstable. We tried to get more conductivity, originally through putting more gel and making sure gel reached the scalp, but then we tried getting extra conductivity by adding water as another conductor! We learned that when the hair is wet, connection immediately jumped to 70-90%!
Update – September 20th, 2019
Well, we realized connection was not present because there was no gel in the capsules! We ordered Ten20 Conductor gel, and will start resetting as soon as it arrives.
Update – September 18th, 2019
Even though the headset is finally connecting, it is still spotty. Connection goes in and out, even in a room without computers, and we have not been able to pinpoint a reason. Once we have connected to EmotivPro, the software connected to the headset, a screen appears in which the sensors appear. Connection percentage was at 0%. We clicked on a tab at the top of the screen that allowed us to change configuration, in order to ensure that the sensors on the screen matched the sensors truly on the headset, in the right spot. We redid the entire headset, but still, 0% connection.
Update – September 16th, 2019
After continued failed tests, we reached a solution! We assumed that the bluetooth wasn’t being picked up, due to the interference with the signal. We then realized that in the WISRD lab, we are, of course, surrounded by computers! There are not only computers, but wifi networks and many servers, all sending signals throughout the lab. If we could get away from signal interference, the data should become clear. So, we moved into a hallway free from computers, and the signal was picked up! With original connection, we can now move into further setup and data collection.
Update – September 13th, 2019
The Emotiv headset had been fully assembled last year, and today was checked and set up with the software. The headset was turned on, and the USB bluetooth drive was plugged into the computer being used, but no signal was being picked up. The headset, EPOCFLEX (F0000090) appears on the screen as available devices, but the bluetooth device is not appearing. When the headset is chosen, a message reads “unable to connect to headset”. After research with no results, as the headset is a newer product, we reached out to Emotiv directly to speak about this problem. They said to refresh the page, and wait, but no difference was made from this update.
Update – September 11th, 2019
White paper #1 is complete! It is focused around the causes of stress in teenagers, and how academic stress in particular impacts learning. This paper was written by Lea B. last year, and I completed a major edit for publication! This will not only be used as a published research paper, but will serve as background in the final research paper that will be completed at the end of this laboratory investigation.
Update – September 9th, 2019
We’re back! After a long summer, we have been working to finally gain access to the new software needed to use the Emotiv headset. I have created a chart to keep track of the deadlines for all research and papers written on the research. I have edited a white paper written last year, that is ready to be published. It will be used as background in our greater research paper on the stress lab. I am also currently writing a paper on previous stress studies, that will be included in the people and places section of the background white paper. Once the white paper is completed, the work testing the product again will begin, and we can follow the schedule to gather data!
Update – April 29th, 2019
We have completed Innovate.ed LA! Lea B., Grace K., and I hosted a 3D printing station where students designed their prints and watched them comet o life. We educated the community about the 3D printing process, and recruited some younger minds to WISRD! It was very successful and I think it can develop into something even greater in the future.
Update – April 16th, 2019
We have been continuously working on the hand. We went through the stringing process, and it is now complete in the build! Now we just have to attach the velcro, and it will be shipped off.
Update – April 8th, 2019
It’s the first day back from break! We are still working on the hand, and finalizing the shape by using the heat gun to make everything fit into the right place.
Update – March 16th, 2019
Assembling has been much more difficult than expected. We are doing some of the molding with a heat gun, and some in boiling water. The PLA either gets too floppy or is too stiff, and there is not an in-between that we have been able to access thus far. We are also putting pins in place, and have had to file them down to fit the mold.
Update – March 15th, 2019
We are trying to put the pieces together. We have everything printed. https://www.youtube.com/watch?v=369PX9LzUPs
This is how to mold the print! It is very difficult, but we are making progress.
Update – March 12th, 2019
We are attempting to print the middle piece diagonally across the build plate with a dissolvable block surrounding it. However, the printer is constantly reading “unable to slice” because the print is so large. After much editing, we finally created a file that will print, but it will take 3 days!
Update – March 10th, 2019
We are trying to figure out how to print the middle part of the arm. It is too big to fit on the build plate. We tried calling a 3d printing office called Kapow! 3d, but they have the same sized printers as we do. We are currently working to develop a way to print the file! It is possible that we can split the file, but then we would have to glue them together, and it may be difficult further on in the process.
Update – March 5th, 2019
We are printing the files on the Ultimaker with PLA. We have the automatic settings on and the print has been successful so far, without supports.
Update – February 28th, 2019
Today, we heated and bent the hand! In order to create a more comfortable hand, we used a heat gun to make the hand pliable. Then, we bent it to the correct shape. We will do the same for 2 other pieces. This hand preaches comfort, so we are working towards a versatile design.
Update – February 24th, 2019
After assembling for a few days, we have learned many things. First, we learned that hand assembly is quite different than our last print. This hand is much smoother, but there is no room for mistakes during assembly.
Update – February 20th, 2019
We have run into an issue, but come up with a possible solution. Our forearm is too big to print on any build plate of any printer. So, after great discussion, we decided to print in a very interesting way. We are printing the piece vertically, with a great deal of dissolvable support. Hopefully, we will be successful! We have edited the piece repetitively and finally seem to have created a solid piece. The print will take over 2 days, so we are hoping it will be correct.
Update – February 14th, 2019
We are printing our next pieces! It is coming along very quickly and very well, and we cannot wait to begin assembly.
Update – February 7th, 2019
The first to prints are completed, and look amazing. We sanded them to ensure that they would be smooth and comfortable. We then removed the old filament on both printers, because there was an issue with the nozzle, that was quickly fixed.
Update – February 4th, 2019
We are printing! We decided to use PLA in gray and light blue for the hand and arm. We are printing on both the Ultimaker 2 and 3 Extended plus, in order to be most time sufficient.
Update – February 1st, 2019
We finally received all of the correct measurements! I cannot wait to work with a different type of hand! We put the measurements into a customizer, and calculated the necessary adjustments we needed to make to the model in order to fit the patient.
Update – January 29th, 2019
Since we are need of specific measurements, we need to make sure that we receive clear photographs with correct placement of the ruler. In order to be sure we are receiving the correct measurements, we needed to send example photos. We were receiving pictures that were difficult to read, and because we need such specific measurements, we cannot begin until all measurements are confirmed.
Update – January 27th, 2019
After some back and forth, we learned that the man will need an elbow driven arm. After taking into account the mobility that he has, we decided to work with the Unlimbited Arm, Version 2. In order to customize this arm, we need a bicep measurement, the forearm length, wrist circumference, and finger tip to bottom of palm length on the hand that has full mobility. We are still waiting to hear back about the measurements!
Update – January 24th, 2019
E-NABLE is up and running again! The forum was updated, and is now working smoothly! We reached out to a man in Texas, and he wants our help creating an elbow driven arm. We are talking about measurements and details with him right now, and cannot wait to move forward!
Update – January 21st, 2019
Continuing to move forward, we wrote our procedure for the next few tests. We are prepping in advance so that we have a complete plan the second the headset arrives.
Update – January 19th, 2019
Today, after the proposal was completed, we continued emailing back and forth with Emotiv. None of their advice on improving our current headset has worked, so another reason for getting a new headset has been confirmed. I also edited one of our white papers today, as we are beginning to had to the background research.
Update – January 17th, 2019
After discussing our plan with the Emotiv team, we learned that they do not offer discounts for the current software. That being said, there is a 15-free-day trial period, and we will only need to use the software for two months this year, from when the headset arrives to the end of school. We have included all of this information in our proposal, which we will make to the board next week!
Update – January 14th, 2018
After emailing with a representative from Emotiv, I learned more details about the new headset and its mobility. The new software processes raw EEG data, and can move mobile. However, we are waiting on a response about a discount!
Update – January 11th, 2018
We are now beginning to seriously focus on our proposal. We are not only making our proposal to learn how to present but in order to lead by example as well. Our proposal consists of a powerpoint presentation with intense research, white papers, and detailed sources.
Update – January 9th, 2018
After some research, we have discovered that the Emotiv EPOC Flex seems to be the best option for a headset that will collect the data we are looking for. We need mobility, as well as accuracy, in order to make a case. After further research, we will propose our plan to the board, in attempt to gain approval for our purchase.
Update – January 7th, 2018
Today is our first day back from break! Over the break, we sent emails out to Emotiv again regarding the stress issue, and began to look into new headsets that would provide more accurate data.
Update – December 17th, 2018
This week, we focused on developing new strategies for our stress tests. Our headset is still not working, and continues to lack mobility. We are currently writing a paper in order to be able to get a different, more mobile headset that would be more beneficial for our research next year. We are also hoping to test stress specifically in a school environment, and relate this stress to the level of work that we have.
Update – December 12th, 2018
This week, we worked to develop a new pulley system for the Emotiv hand. After many trials and errors, we finally developed a system that works. This pulley system has three pulleys stacked on top of each other, making the force put on the motor 3 times less than the original force. With this strength, we should be able to have a powerful hand!
Update – December 6th, 2018
We tested on a new patient today, and were finally able to connect the overall headset, but are still struggling with stress. Apparently, the newer Emotiv designs have been created specifically to fix this issues, which is great, but we are still hoping t develop strategies for using what we have.
Update – November 30th, 2018
After repetitive testing, we are struggling to complete a successful test. We restarted the power on the headset, re-soaked the sensors, repositioned the entire piece, and the stress function still did not work. We then responded to Emotiv’s advice to give the function time to work, and still, nothing! We are continuing to test different factors that may be affecting the work, but so far, we have no concrete conclusions.
Update – November 28th, 2018
This week, our group met to discuss goals for the week and forward progress. We have been in contact with Emotiv, because the stress function on the headset has been unresponsive. We are waiting for a response, and while we are waiting, we have been working on prosthetics again. We have finally updated the hand so that there is an equal amount of force on each flexsor! We are attaching our fully system, and then will test the motor!
Update – November 26th, 2018
Narratives are completing! After finishing this writing, we have come to an interesting conclusion. Our headset has no mobility. If we are attempting to create a headset to determine stress, people will move while wearing this headset. There is no point collecting immobile date because it is completely different from the mobile data that we need. Because of this discovery, we have been researching a new Emotiv headset called the Emotiv Flex. It has more sensors, stronger connection, and would be able to collect data when in motion.
Update – November 15th, 2018
The Emotiv headset had to charge today, so we worked on our other project. We tied the flexsors to the base of the e-NABLE hand, using the piece we had just printed, and then used the soldering iron to put the strings together, and hold them there. Now that the hand is stable, we are working to solve our motor problem!
Update – November 14th, 2018
Today, we worked to set up a lab. We have decided to begin our test with five test subjects. Each subject will be hooked up to the Emotiv headset, and then tested in four different areas. First, the subject must be stressed out. They are then asked to calm themselves down with any method of choice, and that data is recorded. Then, the subject has their stress levels raised again, and attempts the method with deep breathing, calming music, and dark chocolate, using the same previous steps. All data is recorded through film and a screen recording of the graph on the Emotive software.
Update – November 12th 2018
This week, we met with our school counselor, in order to talk about stress relieving methods. We determined that deep breathing, exercise, de-escalating thinking, dark chocolate, music, and meditation are the simplest and most efficient ways of relieving stress quickly. We are currently testing all of these methods, to get data for each test!
Update – November 8th, 2018
After much discussion, we have decided to confirm our projects for the year. We have two major research and design projects for this year. Our first project is designing a stress reducing test. We are using the Emotiv headset and attaching it to an earpiece, that will beep when stress raises too high. Then, we will have another system explaining stress reducing techniques, so the individual can reduce their stress again, and the piece will stop beeping. Our nest project is regarding prosthetics, and connecting these prosthetics to the headset as well. Essentially, controlling them with your mind. We can’t wait to write about everything!
Update – November 6th, 2018
We had our poster presentations last night! Our combined e-NABLE/Emotiv group explained all that we have been working on, and designed a poster filled with background, abstract, etc., to provide physical evidence. We talked about our progress throughout the year, as well as how the combination of the two teams changed the project. For our demonstration, we attached the Emotiv headset to a test subject, and allowed the audience to talk to the subject and watch the way his brainwaves changed during their interaction. We then switched the headset to recognize facial motion. The face of the test subject was analyzed by the program, and when the subject winked, the face on the screen would wink, when the subject smiled, the face on the screen would smile as well. It was a huge success, and we can’t wait to continue developing our knowledge and growing the lab!
Update – November 3rd, 2018
After completing the hand last week, we learned that we had to develop a piece that would attach each flexsor, with equal force, to the middle of the hand, so that the motor could be attached. After trial and error, we developed a piece that will get the job done! Below is a photo of our design.
Update – October 30th, 2018
Dark Matter Day was a huge success! There was major student involvement, younger students showed interest in science and technology, and it was an overall educational and fun-filled event. Check out the WISRD twitter to see footage from Dark Matter Day! https://twitter.com/WISRD?ref_src=twsrc%5Egoogle%7Ctwcamp%5Eserp%7Ctwgr%5Eauthor
Update – October 27th, 2018
We completed our redesigned Emotiv hand! We are currently working to design a pulley system to connect the Emotiv motor to the flexsors of the hand, so the fingers will bend when an emotion is present. Below is the redesigned hand!
Update – October 24th, 2018
Everyone has been assigned tasks for DMD! We have a widespread variety of activities, as all of WISRD must be represented through the event. All WISRD members will be involved this year, creating more connections across grade levels and labs. Attached is the assignment list, so all of the awesome games can be seen.
Update – October 23rd, 2018
We’re planning for Dark Matter Day! Last week, I went to the lower campus to make an announcement about our event. It was wonderful to see so many younger kids interested in WISRD, and we can’t wait to continue planning!
Update – October 19th, 2018
As I’m learning how Emotive works, I am still working with similar designs, as I’m helping to construct the hand associated with a motor connected to the Emotive headset. The hand was previously redesigned, so not all of the parts fit together. I spent most of my time reconstructing the hand, and filing down parts that were too stiff.
Update – October 18th, 2018
During the construction process, Lea and I began to work closely with the Emotive team. We helped test the Emotive headset, and I learned about programming the device as well. As the e-NABLE program is still under reconstruction, we are going to be working with Emotive for the time being.
Update – October 17th, 2018
Today, we worked to connect the lights and wires to the printed lightbox. It required wiring and precision, and a great deal of collaboration. Below is a photo of the backside of the lightbox, with lights and wires attached.
Update – October 15th, 2018
After many redesigns and updates, I finally have completed a strong lightbox. We are testing a new type of brain function, where four emotions can be tested. The emotion that the light is associated with will light up when that part of the brain is activated. The design can be seen below!
Update – October 8th, 2018
We’re still waiting for our new filament to arrive! Since the e-NABLE forums are being redone, it has been really difficult to communicate across these platforms. While we are in limbo, we have decided to work with the Emotive team! We are helping to design a new hand, as well as learn the processes behind the Emotive designs.
Update – September 26th, 2018
Aside from having the mission statement of each WISRD project on our website, we now have an area in the WISRD lab where these statements are projected. New and veteran WISRD members, along with visiting scholars, can check the board for updates on what is going on in the WISRD labs at any time. It’s a great way to keep the community all on one page!
Update – September 24th, 2018
Unfortunately, the flexible filament that we tested with was not quite flexible enough. As we await the arrival of the new filament, we are working on writing articles for the WISRD magazine. I am currently focusing on the psychology behind criminal behavior, and the information I have found is quite astounding. At the same time, as October approaches, we are beginning to plan for Dark Matter day again. We are hoping to involve as much of the upper school as possible this year!
Update – September 20th, 2018
We have new filament! We completed a test print with the flexible filament, and learned the extent of its flexibility. It can only be pushed so far, because it snaps if the pieces are thin. We are printing another test hand to see how it goes! Below is an image of my project partner, Lea Bond and me, with our original printed hand, while we were learning how to control the new printer.
Update – September 13th, 2018
Good news and bad news… The good news, is we finished the print. The bad news, is that we used the wrong filament. Every other print used the same PLA filament, however, this hand asked for a strange type of filament that we hadn’t used before, and did not have in stock. The description of the new filament, called Ninjaflex, was described as similar to PLA, but slightly softer. However, once we started working with the hand, we realized that was not the case. Ninjaflex is completely flexible, and can bend in half, and PLA most certainly cannot. This is a great learning experience, as we tried to work with what we had, but it does not always work out. We are going to print a different hand instead, due to the difference in material, and we will work from there!
Update – September 11th, 2018
After working with the new printer, and completing the majority of our prints over the weekend, all pieces of the hand should be done by the end of tomorrow. Once the prints are finished, we will begin assembly. The water soluble supports have made the prints smoother, more structured, and amazing to work with. I am beyond excited for the upcoming hand construction!
Update – September 5th, 2018
Another amazing program that I learned today is called TeamViewer. It allows me to print to the wireless printer and monitor these prints from anywhere. I can cue prints, line them up so there is always more to print, and each print will not begin until the last print has been taken off the build plate with verification. This will allow a much more efficient and faster printing process, and will be helpful to the overall printing world with future events.
Update – September 1st, 2018
The base of the hand is complete! The new printer is incredible, and the water dissolvable filament we used to print supports has left us with the smoothest hand.
Update – August 28th, 2018
We’re working on another hand! As we continue to communicate with individuals about their specific questions surrounding hand manufacturing, we have decided to increase our own knowledge of the subject as well. Last year, we printed the Raptor Reloaded hand, and this year, we are printing the most complex wrist powered hand, the Flexy hand. This model contains more finger joints, smoother prints, and a rounder design to replicate the image of a human hand. We are printing with our beautiful new Ultimaker 3 Extended, which we set up recently. We learned about new technology that allows the printer to connect to the computer through its own network, instead of including the confusions of USBs or SD cards. This print is much more detailed, so will take longer to print, but will provide us with greater understanding of all e-NABLE projects.
Update – August 27th, 2018
Along with continuous communication with members hoping to join our chapter, we hope to work with a new hand design, to increase our understanding of the products. I will also be running the Instagram account in attempt to reach a wider audience.
Update – August 24th, 2018
As board members this year, Lea and I don’t only manage our e-NABLE program, but the 3D printers and training new members to use those printers, as well as helping out the overall WISRD community. Last week, we spent a great deal of time designing and installing a bulletin board that will help new member orientation, as well as overall organization. The name of every lab, a short description, and the members present are up on the wall for all to see and add to, to increase communication between classes. Throughout this process, I worked with new tools, such as a stud detector, that will continue to be helpful throughout my life, but was a product I had never worked with before!
Update – August 22nd, 2018
Welcome back to a new year of WISRD! Over the summer, we have been communicating with many people who would like to be involved in e-NABLE. As we are our own chapter now, we can add members to our chapter to collaborate on various projects. We are currently in the process of adding both some assemblers and some designers to our team. As our chapter grows, the more people we can reach to help the community!
Update – May 16th, 2018
Today we printed another piece for the Aerodynamics team. We printed a drop launcher for the bottle rocket as a prototype, and will make adjustments as necessary.
Update – May 14th, 2018
We have been working on our reflections! As the year comes to an end, we are noting all of the work we have done this year, as well as reflecting on what we can do next year, so we can pick up quickly at the start of the new year.
Update – May 9th, 2018
Today, I printed a major piece for the Aerodynamics Lab. I made rails for the anemometer to be attached to the wind tunnel, and I printed 9 separate pieces that were attached to each other through a peg and a hole. Below is one of the pieces printed.
Update – May 7th, 2018
The Lulzbot Taz 6 is finally printing again! After a difficult break where steel filament had gotten stuck on the way to the nozzle, we had to remove the filament and reassemble, only to learn that the heating system was fried. We had to rewire the entire printer, order many new parts that took a long time to arrive, discover new methods of reassembly since the printer had shifted, and put it back together. Finally, it is ready to use again, which will benefit all labs greatly since it has the capacity to print larger and in different materials.
Update – May 2nd, 2018
Finally, after over a month of waiting, we have gotten responses from people in need! We emailed with individual whose wife lost both of her hands at the beginning of the year. We are hoping that we can be of service to this family, because it would greatly benefit this family as well as our learning! We also have been in contact with another individual from e-NABLE who may be able to help us get in contact with other people in need. We cannot wait to continue!
Update – April 30th, 2018
We had our poster presentations today! They were incredible, we heard from a wonderful speaker named Dean Ho who encouraged our work and gave us pointers for publicity, as well as teaching us more about the world of medicine and business. We spoke with many individuals who had connections to people in need, and we are hoping to work with some of these individuals in the future.
Update – April 22nd, 2018
Today, we tried to print with the ceramic printer. However, because the clay had been sitting in water for over 24 hours wrapped in a cloth, the cloth had molded. The mold had worked its way into the clay, and had quite a strong stench. This made the texture of the clay inconsistent, and messed with the print. However, we are re-soaking the clay, and will print again in the next class.
Update – April 20th, 2018
Along with finishing our poster, we reprinted anemometer parts for the Aerodynamics Lab, in a much larger size.
Update – April 19th, 2018
We have been working on gathering information for our Poster Presentation! Ours is centered around our detailed study of printing in different materials, and focuses on the important aspects to take note of before printing in each material(bronzeFill, brassFill, steelFill, woodFill, ceramic), as well as the necessary temperatures and extruder settings for each material.
Update – April 16th, 2018
After beginning the reassembly process, we realized that we needed to order another part. We need a 4mm star lock washer, to attach the heating wire to the extruder head.
Update – April 12th, 2018
We have been working on fixing the TAZ 6 printer. A new thermistor and extruder head were necessary, because the wires leading to these pieces were fried and disconnected. I took out the old wires, fixed the pin-head attachments of these wires, replaced the wires, twisted and reattached them, and am currently working on reassembling the printer. Below are images of the printer being assembled and the new parts being attached.
Update – April 10th, 2018
While working on the Anemometer Project under the Aerodynamics Lab, I printed a model Anemometer and sliced the print to fit the calculations. Once the model is completed and tested, we will print a full sized anemometer with a motor that will work with the wind tunnel to gather data on wind speed.
Test Anemometer
Update – April 9th, 2018
Over Spring Break, while we have not had access to the WISRD Lab, we have been working on a new presentation. Our goal is to teach the surrounding community about metal prints. Because it is a newer development, many customers and inquirers do not know about this advancement, and it is important to spread the word because it is truly revolutionary to the 3D printing world.
Update – March 21st, 2018
We have made requests to be an assembler on multiple projects, and are waiting to hear back from the people in need!
Update – March 19th, 2018
We have been communicating with e-NABLE volunteers, and have gotten new information about how to figure out our next assignment.
Update – March 16th, 2018
Steelfill is much more brittle than bronze and brass, so the filament tends to snap before a print is completed. We had to take apart and reassemble the printer, and are working to develop a new method of printing with this material.
Update – March 15th, 2018
We worked with our first steelfill print today! We discovered that the extruder should be set to 230˚, and the bed should be heated to 60˚. The wipe temperature must be lower in order for the nozzle not to burn through the material it wipes on. Our next print will be brassfill, and then we will have printed all of the metals and plan on working to uncover which metals work best for what types of prints.
Update – March 14th, 2018
All of our printers are up and running! Both Makerbots, the Lulzbot Taz, and the Ultimaker! We are currently studying what printers work best with which filaments, and have figured out how to slice prints properly on the Lulzbot Taz as well.
Update – March 9th, 2018
We worked with the clay printer again today! When clay becomes too hard (even if it feels soft to the touch), the printer will not extrude. We took notes on on the necessary consistency of the clay, because after taking out the clay today, we learned how difficult it becomes to work with once it becomes too hard. We have a better understanding of the necessary consistency, and this will help us greatly with our future endeavors!
Update – March 7th, 2018
After our second attempt to print in bronze, we learned about a new Cura program used on the Lulzbot Taz. At first, there was wood filament from the previous print left in the nozzle, and because the heat settings are different to print with metals, there was trouble extruding. Then, the print was sliced incorrectly, and the print was too dense. However, after making corrections, a skull was printed successfully, and we are currently learning different polishing and buffing techniques for future prints of higher importance.
Update – March 5th, 2018
We learned a new software last week! Using the Kinect software from Xbox, through a program called Skanect, we took a scan of a face, simplified and edited the settings, and printed it! This could be revolutionary to the art industry of sculpture making, and we could print busts in bronze that can be even more detailed and accurate than statues.
Update – March 1st, 2018
Another ceramic print was completed! After attempting to print this soap bottle and having errors with the printer, but after running it through Simplify 3D, the project ran smoothly.
Update – February 28th, 2018
WISRD has been officially approved as an e-NABLE chapter!
Update – February 26th, 2018
After learning that the attempted print last week failed because of the consistency of the clay, a new method was applied in order to moisten the clay to make it stickier. After soaking the clay in a bin with water and wrapped in a wet cloth for 12 hours, the clay was perfectly sticky.
The sticky consistency of the clay is visible through the tube.
The solid base is because of this new consistency.
Update – February 20th, 2018
The ceramic 3D printer has been under frequent use recently. After each use, new information on how to best manipulate the settings is discovered. We learned that the extrude speed must be turned up to around 200 in order for the base to be laid down.
Update – February 14th, 2018
Today the first bronzefill print was completed! We learned that the nozzle must be heated to 215˚ and the bed must be heated to 60˚. The print was successful, but understandably, it takes longer for the filament to heat. During the first few rotations, no filament came out of the nozzle. Then it came out in dribbles, and finally, it began to fully release filament. We must figure out a way to heat the printer for longer before prints begin, because once we print more complex objects, any mistakes could ruin the entire print.
Update – February 9th, 2018
We are making our first attempt at printing with bronzeFill! We are developing new settings and processes to print with metals. In our first attempt to print in bronze, we realized that there was a difficulty in transferring files. We learned that files are transferred differently to the SD card when printing on the Lulzbot Taz, because the Taz is must have objects printed from the card and never from the computer.
Update – February 6th, 2018
We successfully completed our first woodfill print today! Interestingly, the settings on the printer did not need to be changed in order for this print to work, and we will continue to print and explore the settings that provide us with the best results for different materials. We are also currently in the process of writing an article about the machine settings.
Update – January 29th, 2018
The Lulzbot Taz is back in action! It hasn’t been used for a very long time, and now we have access to much larger and complex prints. It will help us greatly as we continue with our e-NABLE prints, and collaborate with other WISRD teams in the future.
Update – January 26th, 2018
We began working on fixing the Lulzbot Taz 3D printer, and discovered that there was filament stuck in the extruder, as well as a wire that had come disconnected. We disassembled the printer, used a soldering iron to heat the extruder and extract the filament, then soldered the unattached wire, redid the electrical tape for safety precautions, and reassembled the printer! It will be tested at the beginning of class next week.
Update – January 24th, 2018
The ceramic 3D printer has been up and running, and today I learned how to fill, assemble, print, and modify print settings. We attempted printing with the largest nozzle we’d ever used, and learned that in order to print with such a wide nozzle, it is necessary to extrude the clay much faster. We also developed a new strategy to print, using a dry board instead of wet paper, because it solidifies the base. We’re trying to learn a new software that simplifies prints so we have a wider range of options that work with the ceramic printer. Attached is a video of the printer at work! IMG_5791
Update – January 16th, 2018
E-NABLE has replied to our forums page, telling us that we have been approved as a chapter! We are extremely excited! Our Credly badge has been sent through, and once the email has been received, we will begin getting new hand orders.
Yesterday, I also used how to use Textedit and developed an understanding of the process behind it. So much code goes into writing even just a word, because in Microsoft Word for example, font size, spacing, font, headers, etc., go into the coding process. When writing on Textedit, you are writing straight code without the other unnecessary pieces of code involved as well. I will take this learning into future coding, especially as it has to do with 3D printing!
Update – January 6th, 2018
We looked at the credly badge we plan on claiming, and it wants evidence attached in order for us to claim it. Here’s the link to the badge. We posted a video we made of the hand and attached it to the forum. Here’s the link to our post.
Update – January 3rd, 2018
As we start 2018, we have made some goals. The first one is to get approved in January, so we can start the year off making hands. The second one is to make at least 3 different types of hands in 2018. And our third one is to focus on the hands this year and try to keep the 3D printers up to date and maintained so we don’t end up having to focus on fixing them.
Update – December 14th, 2017
Today is our last class of 2018. We leave e-NABLE with a plan for next year. We started filling out the form, and the only space we have left to fill out is our credly badge, which is a badge that gives us approval for becoming a chapter. We will continue this in 2018.
Update – December 11th, 2017
We just found a website where we can request to join the chapters map. We plan on filling this out next class. Heres the link to it: here
Update – December 4th, 2018
A new narrative and reflection process has been presented in the institute, and there has been much success under these new standards. After writing reflections, we have continued to work on the long application process. We’ve filled out all the forms we can, created a youtube and our introduction video, been very active on twitter, joined the e-NABLE Google+ community under our new email, and completed a different form of request for becoming a chapter. We have also been in direct contact with members of e-NABLE, and they are following us on our Facebook page. Since our video is up, it is now pending approval again!
Update – December 7th, 2017
In a final check of the hand, it became clear that there was a more efficient way to attach the velcro than the way previously attempted by following the instructions on the e-NABLE website. I undid the screws and velcro, trimmed the velcro pieces, and reconstructed the velcro attachment. Lea B. and I have been in contact with the e-NABLE team, are filling out paperwork and have sent in all of our images, so if all goes well, our hand should be verified quite soon.
Update – November 29th, 2017
The hand is finally fully complete! Since the printer is fixed, we went back to reconstruction. One of the flexsors broke when somebody was handling it, so I took it off and restrung this finger. Then, I superglued all of the elastic, and attached the velcro with bolts we shortened. I threaded through two more pics of velcro, attached them so they formed a cone-like shape inside the palm, and now we are ready to submit are hand! Our goal is to get verified to be able to print for people in need of a hand in our community, and if our test hand is approved, we will be able to do just that. Throughout this process, I learned that you have to look at problems from many perspectives in order to come to a final solution. Although I was disappointed at first when the flexor broke, because that meant redoing the entire stringing, knots, and attachment, it was a learning process and I’m very glad it happened. It taught me to always double check models to make sure they are sturdy before somebody in need attempts to use them, and to be ultra efficient from the start so a process does not have to be redone. Now that we know how to fully construct the hand, future hand construction will be a much shorter process.
Update – November 27th, 2017
The Makerbot is fully fixed! After the new extruder arrived, we took out old wiring and rewired the new piece to the printer. The first object since the fix was printed today, and went smoothly.
Update – November 13th, 2017
WISRD just got a ceramic printer, and we assembled it this past week. Some of the parts are 3D printed, and it is much larger than all the other printers we have. However, printing and design is done the same way. Files can be designed or found on Tinkercad or Thingiverse, uploaded to the SD card, and printed. This printer takes clay, condenses it around the threaded metal piece passing through the center, follows the design, and once the print is complete, it just needs to be fired. We learned it is important to be careful of air bubbles in the clay, because they can throw the printer off track. Attached is a photo of the 3D printing team who assembled the ceramic printer, and more videos of the printer at work can be found on WISRD’s Twitter.
Update – October 27th, 2017
The Makerbot printer has been fully taken apart. The filament got stuck in the tube between the nozzle and the heat bar of the right extruder. First, we attempted to loosen the filament by tugging on one end with pliers. Without success, we decided to disassemble the right extruder. We removed the nozzle and gave it an acetone bath to remove the clogged filament. We scooped out whatever hardened filament we could, and then used a soldering iron to melt the filament and remove it from either end. The issue was that the heated plastic cooled too quickly, so once the solder was removed, nothing could get through. We attempted multiple other strategies with no luck. A new extruder was ordered and we are currently assembling it onto the Makerbot.
Update – October 14th, 2017
InnovatED.LA was a huge success! It was the most incredible experience. As mentioned before, I led a 3D printing workshop. We gave a quick presentation, and then the learners went straight to work. Many children attended this workshop, and their minds were blown. They designed whatever object they wanted, and they were beyond excited when they finally got to hold the objects that were just figments of their imagination, in their own two hands. It was so inspiring to learn that there are so many people, young people, in the world who care about making a change in the world for the better. Speaking with these kids and watching them get excited to learn gave me hope for for a much brighter future. I received a text after the workshop, from a woman saying that I changed her daughter’s life, and these skills would be something she held on to and what she aspired to do. To know that I made an impact on someone’s life, someone who will do magnificent things, that’s a feeling that’s truly life changing.
Update – October 8th, 2017
The clogged Makerbot was a lot more complicated to fix than we expected. The filament is stuck all the way down through the nozzle, so we cannot simply remove the filament. We are disassembling the printer.
Update – October 4th, 2017
Because InnovatED.LA is coming up on Saturday, October 14th, the work on the hand has come to a short pause. Along with the other current e-NABLE members, I will be presenting a project on 3D printing for beginners. Visitors will be taught how to create their own designs on a program called Tinkercad, and will have their objects printed before their eyes. One of our 3D printers is broken, so all our time is being dedicated to fixing it before the event so people with be able to experience InnovatED.LA to its utmost capacity.
We’ve made a significant amount of progress on the printer. The nozzle was clogged, and in order to clear out the nozzle, it must be disconnected from the rest of the printer. This requires a lot of deconstruction, and since we have finally freed the nozzle, we just need to soak it in an acetone bath and reconstruct what has been taken apart.
Update – September 20th, 2017
The hand is completed! Now we just need to attach the velcro. We drilled holes in the velcro, and we have been testing different screw sizes. We know the necessary diameter of the screws, but we don’t have the correct length. Once we obtain more of these screws, we will be able to complete the velcro attachment.
Update – September 13th, 2017
We successfully replaced the direction of the screws, but today we noticed that there were issues with the finger joints. When 3 of the fingers were bent down, they did not snap back up. We realized that it was’t the tightness of the elastic that was causing the issues, or that the joints were not lubricated enough, but that in the printing process, some of the inside joints were printed thicker than others. In these joints, tiny ledges were printed inside the joints that created too much friction for the fingers to move back into place on their own, because they would stick to the ledges. We took apart the fingers, filed the joints, and then reassembled the fingers. IMG_4640 2 As you can see in the video, the ring finger is still incorrect while the rest snap back into place.
Update – September 11th, 2017
The screws that connect the string from the palm to the forearm were put in incorrectly. They were put in so that the holes faced each other, instead of facing out. We are currently fixing them by rescrewing the bolts.
The top one is screwed in the correct way, while the rest are not.
Update – September 7th, 2017
The piece that we are currently working on should end up holding a screw based on the original plans. However, the screws are cracking our pieces, and bolts have proven to be very stable and more accountable. We are creating threads so that we can twist the bolt into place without any cracks.
Update – September 6th, 2017
After reprinting the hand, we decided to stretch the holes using a screwdriver. We connected the forearm to the palm successfully, and are now working on attaching the flexsors to the forearm.
Update – August 31st, 2017
Today we were assembling the hand, and the holes in the side of the hand were too small for the pins, so when placing the pins in the hole, the forearm snapped and we are currently reprinting it.
Update – August 30th, 2017
The wrist portion of the hand just finished printing. We took out all the supports and then once we attach the wrist to the palm and thread the flexsors through the wrist, the hand will be complete. We’re going to start updating our e-NABLE page with instructions for the next class, because all WISRD members on this project are working at different times.
Update – August 27th, 2017
This year in WISRD I am going to be working with Lea B. and Grace K. on an e-NABLE project. I’ll also be learning how to 3D print.
Bibliography
“The Raptor Reloaded.” Enabling the Future, enablingthefuture.org/
upper-limb-prosthetics/raptor-reloaded/. Accessed 13 Sept. 2017.