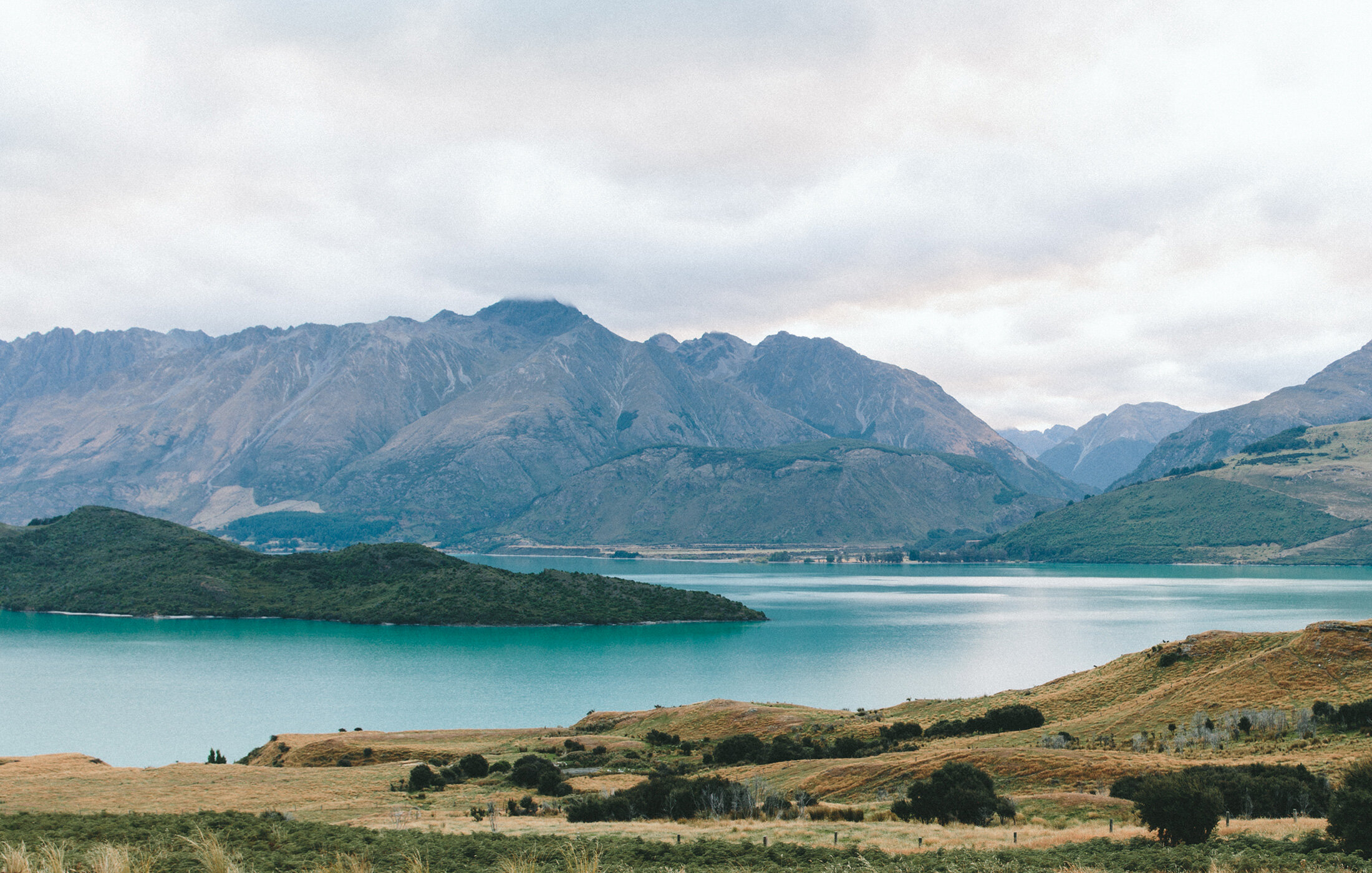
Felix
Posters for Fall 22 and Spring 23
Despite the website being down for half of this academic year, much progress was made on my project this year. Click the icon to read the posters for the WISRD Physiology Group this year, as well as posters from past years.
Journal entries imported from the previous iteration of wisrd.org
FELIX
Weekly Journal Entries for Felix in the Wildwood Institute for STEM Research and Development
Please note hyperlinks will not be available in printed versions.
Additional work can be found under the Lathe, WISRD Shop, and Spider Robot pages.
March 19, 2018
The RFID parts have come in so we can start testing the system with our servers and see if we can figure out the active directories of the WISRD server. I am hoping to meet with Ferdi and William to discuss the layout, programming, and project development for the next few weeks. Using the server and its presumably programmed credentials, we will have to map out every WISRD member’s qualifications and in turn also create a graphical interface.
March 12, 2018
It seems that each day goes by faster and faster. With the shop getting organized and everything returning to regular order, I took inspiration from an Inventables project to improving our shop further. Hopefully working in tandem with William and Ferdi we will design an RFID secure system. This system seeks to address the concerns over liability and safety of heavy machines and accountability for delicate tools. The system will be built before the three institute members involved leave, however, one of the parts is unavailable for an unknown period of time.
February 22, 2018
As it has been a short week within the Institute, I solely focused on the maintenance of the 3D printers and assisting others with their print jobs. Abe and the Spider Robot group have continued their printing of legs and the respective ligaments for the articulated design which I consulted for. Outside of the realm of 3D printing I have continued my own research into the process of recycling 3D prints and materials. It appears that in the time I have left within WISRD I won’t be able to complete the entire recycling process, but may get the first of three done.
February 5, 2018
Once again focusing on the process of recycling our old and wasted 3D prints, I have been investigating the various steps of this possible program. From reading through various DIY projects and blogs, it appears that other than purchasing a commercial or industrial grade grinder, we will need to build our own grinding machine that will reduce prints to a powder that can later be pressed into a pellet form.
January 29, 2018
Below is the finished and in-use housing that I printed the end of last week. I manipulated the buildplate heat settings for this print in order to guarantee that there would be no warping as this piece must align with others almost exactly.
In addition to assiting with 3D prints, I have been doing research into the process of recycling old, incomplete, and other prints to reduce WISRD’s environmental impact and promote sustainability. Over the past three times my WISRD rotation has met, I have counted roughly 20 prints that were never finished, have been discarded, or are otherwise laying around without a purpose. Looking into the benefits and drawbacks of recycling and extruding our own filament, I have found that there are sustainable and efficient ways of going about this process. I believe that I have a reliable means of extruding a final filament, but do not yet have a way of grinding old prints to a consistent size pellet that will feed the extruder.
While not my current concept, I initially used this DIY extruder idea to brainstorm further: https://www.youtube.com/watch?v=F6ryVn9SL4I
January 25, 2018
Once again assisted in a print for the Spider Robot project.
Spiderbot Breadboard housing
September 4, 2017
In tandem with Abe, I took a leadership role in guiding the helicopter and plane RC/VR project. As it has evolved, the two of us have continued to spearhead the design, development, and reporting of the project.
March 14, 2017
Working on the lathe has required a constant focus and therefor caused a lack of journal entries. While working on the physical lathe, I have simultaneously been writing a guide and standard operating procedure for the whole WISRD shop which will be linked in this page in the near future. With the help of Marvin from UCLA, Will, Blake, and I have successfully been able to create threads on the lathe. The first application of this was used on threading PVC piping for the hydroponics team. Because of irregularly sized piping, we had to custom cut and thread the ends of the PVC. Using the lathe we were able to achieve 14 threads per inch without any issue!
September 13, 2016
The past three weeks, I have been working on our lathe project, leading the restoration and focusing on the gear system maintenance. Last weekend, I got the chance to meet _____, who restores lathes, cars, and ____. Blake, Will P. and I discovered a broken tooth on one of the main gears for changing directions last week and Joe and I went to ___’s shop to have the gear repaired.
April 17, 2016
With the end of the year closing in, I have begun to read and ask around the institute about how the MOU (Memorandum of Understanding) learning format has influenced learning outcomes and the institute model. This idea has been guided by the work that Ella and I have done with both GameDesk and SmalLab which have been partnerships between WISRD and the stated organizations. More to come.
March 20, 2016
This week, I continued working on the GameDesk collaboration and have been in the process of creating my ideal learning product for the next meeting. In the process, Ella and I have been taking the good aspects from various apps, websites, and programs to create a visual for what we envision the product looking like.
January 31, 2016
Replaced the rear shock on the golf cart as well as looked at the leaf spring (as seen here). We have overall just done some maintenance on the golf cart – cleaning motor, brake, and accelerator parts. As we cleaned the accelerator parts, we discovered that the contacts that produce the various speeds are either damaged or missing. Apart from this, we noticed that while changing speeds, the contacts in the entire accelerator module have a tendency to spark. This caused by the fact that there is a missing piece that sits at the bottom of the accelerator that acts as a guide for the accelerator.
January 24, 2016
With a golf cart in the garage of the building, Harry, Max, Ella, and I decided to take a look at the wiring and electronics of a electric golf cart to see what our final project may require. The first thing that we noticed was that there were quite a few parts that we did not understand, for example what a solenoid is and does. As we learned, when a car is started, an electric current passes through the solenoid, which in turn closes two heavy contacts and creating a current strong enough to start the motor. After most of the wiring was completed, we started the golf cart with success. We have at this point not yet wired our lights as there is a broken fuse for where the wiring will come in contact with the batteries.
January 19, 2016
At the beginning of the week, we looked further into developing our go kart project, by researching a steering system. I looked into various steering mechanics and how they function. In the end, we looked at the mobility each steering system gives us and how fast the go kart will go and decided that a rack and pinon system would be the best.
Although we did look into the go kart project, my attention was moved back to the SmalLab project as we further developed our idea for teaching K-3 students how to find the perimeter of various shapes. We have moved into testing how various digitally created designs appear in the Unity software.
January 11, 2016
The past week, Max, Ella, Harry, and I brainstormed a new project for the second semester of work in the institute. The outcome of the brainstorm was to design and build either an electric or gas powered go kart. The idea came from various Instructable workshops ideas that we worked to make our own (Workshop Ideas). To start off the project, we have split up and begun to look at different components of a vehicle. I myself have researched the various differences in electric motors and gas powered engines (I began here). While the decision between electric vs. gas power is still being discussed, a portion of the research has gone into understanding what other components are necessary. If we were to take the electrical approach, we would have to acquire motors with enough torque to propel a tubular steel frame forward. At the same time we need to find batteries that have a DC current as these motors do not accept AC. To build the go kart frame, we will use our newly acquired skill to arc weld (specifically MIG welding) the frame and any other components.
Meanwhile, SmalLab Learning has contacted us with a “work in progress” MOU. Will and I are now tasked with creating an interactive game that will teach younger students about the perimeter and area of shapes. Ella has joined the team in developing the concept for the game. Currently the game is in the first stages of designing the background and base script for the game to function. Ella is working on creating the background, which will be a garden where students can drag in different plants and vegetation plots, which in turn will change the perimeter and area of the garden. I have spearheaded this project and have to learn different leader skills as I have to keep certain members on track and make sure that each portion of the project is completed. I am figuring out different coding elements of the SmalLab game as we are creating this game from scratch. We have encountered some difficulties as Unity uses its own code (C++ and C#) as the only way to learn this form of code is by looking at online forums. Our plan is to figure out how individual tiles (various vegetable/fruit/plant plots) on a grid may be manipulated by students to form shapes (either preset by the teacher or created by the student) that they can then use to identify the perimeter. Once we have finished the rough draft of the game, we will hopefully test the game (without movable parts) in the actual SmalLab space.